Outsource manufacturing challenges
Sourcing elite factories and ensuring superior quality is complex and costly.
Vetting factories, communicating product requirements and negotiating price.
Designing product inspections, executing quality control processes and reports.
Hiring employees, managing production and operations with multiple factories.
WHAT MAKES AIRBATCH PLATFORM POWERFUL
Reduce costs and increase margins with factory direct pricing and work automations.
Our platform works out of the box, instantly connecting data and automating workflows.
Connect directly with elite factories that will reduce product cost and increase quality.
pass rate
Our platform designs quality control processes that average a 98% inspection pass rate.
on manual work
Replace manual sourcing and quality control work with AI automations.
SCALE QUALITY
Product Sourcing
Collaborate directly with elite factories to reduce product cost and increase quality.
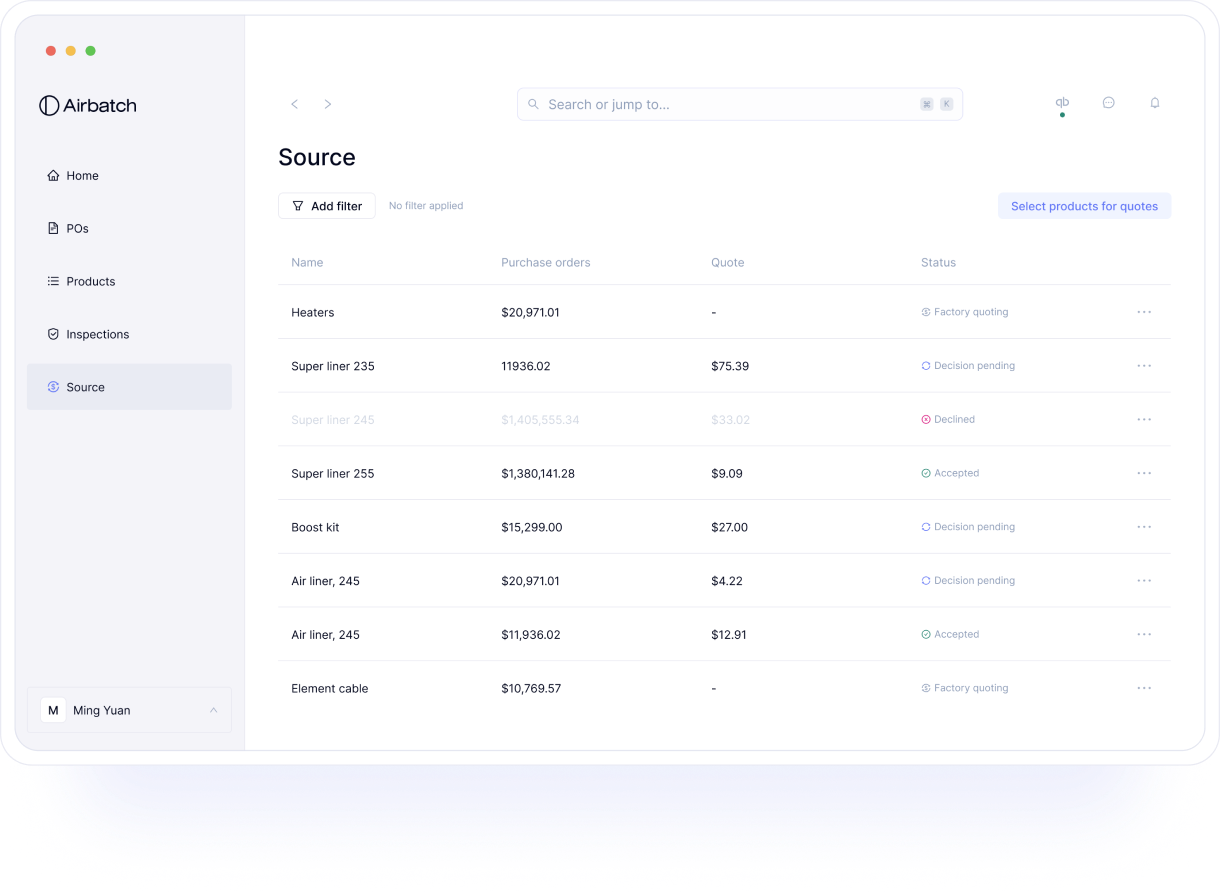
Quality Control
Leverage real-time data during production to insure only quality product ships.
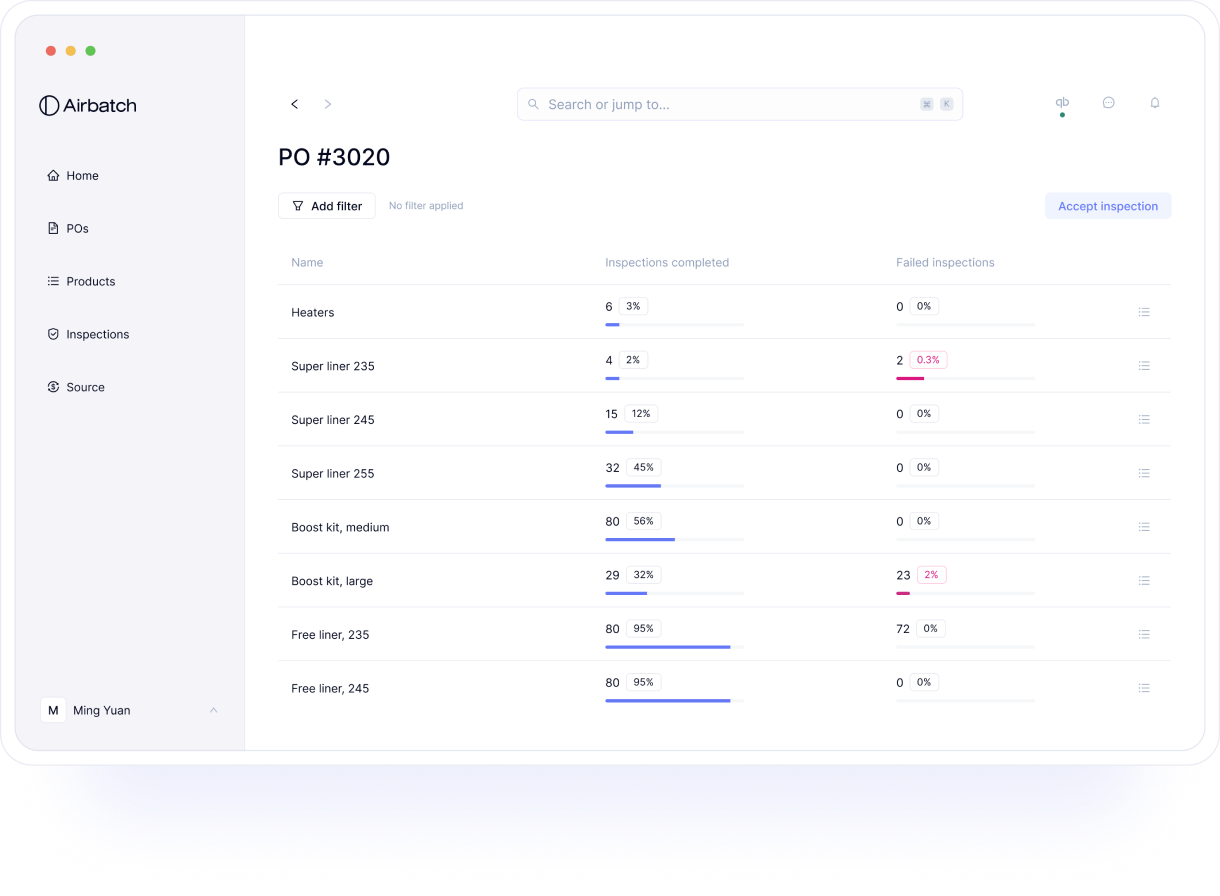
AUTOMATE WORK
Data Integration
Integrate accounting and ecommerce platforms to automate data sync into Airbatch on factories, POs and products.
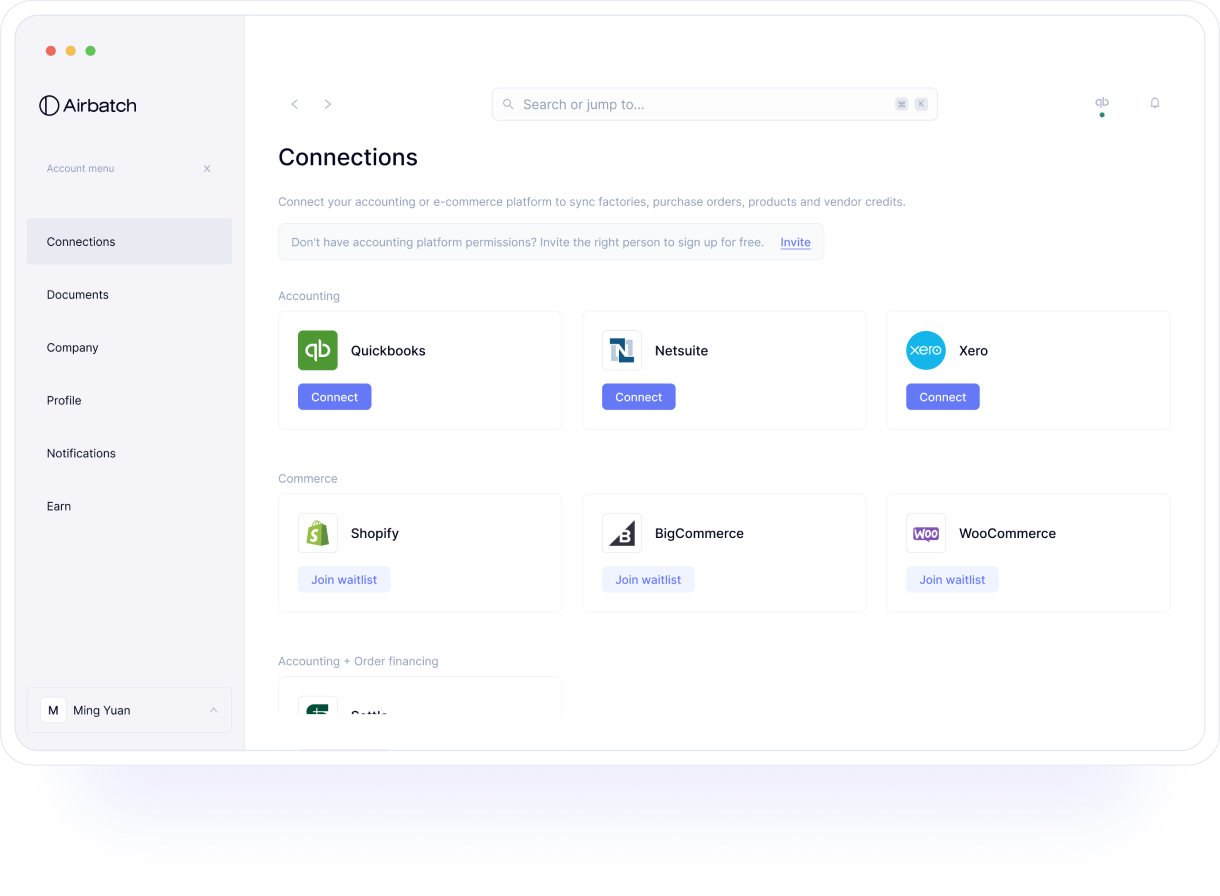
Real-time Alerting
Work directly with factories on sourcing and quality control with real-time alerts and critical change logs.
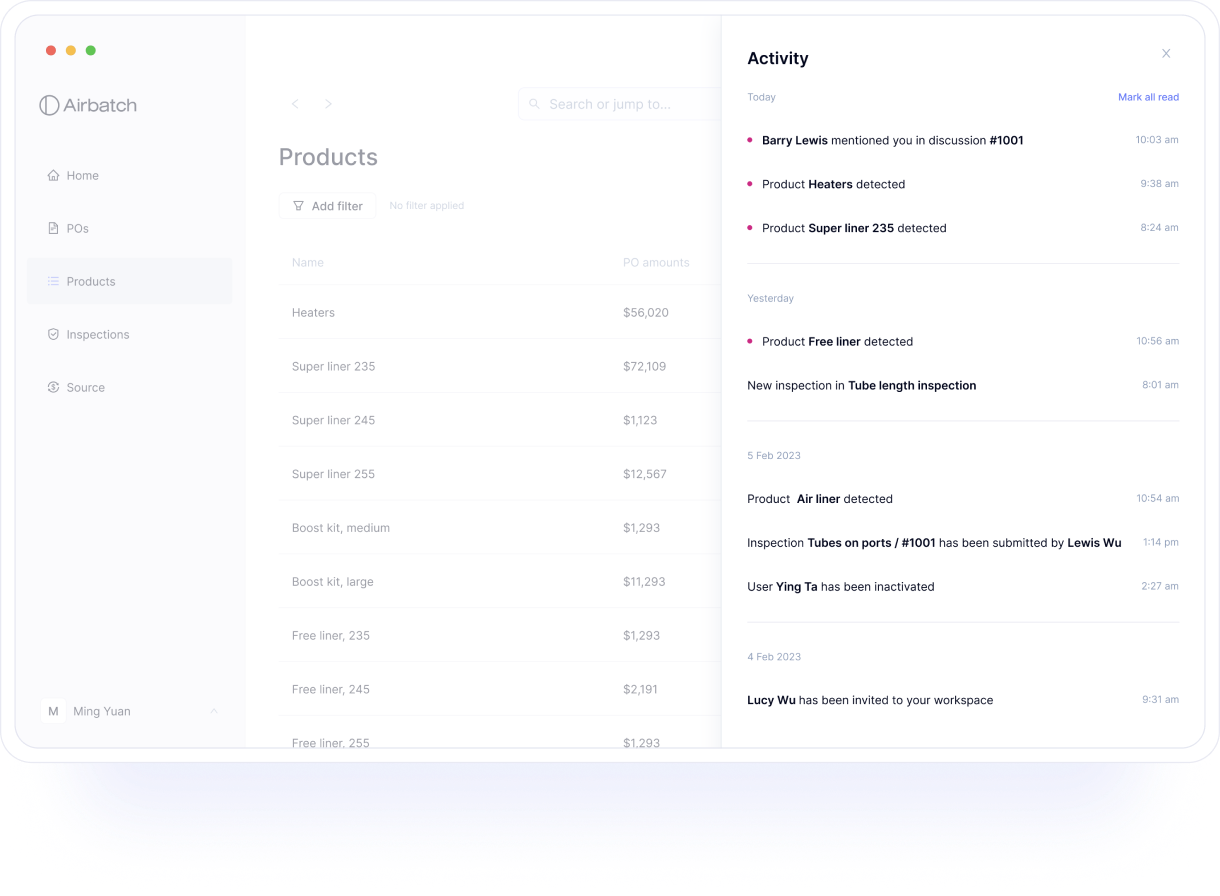
AI + ML
Enable AI to update future purchase orders with product inspection parameters gathered from machine learning.
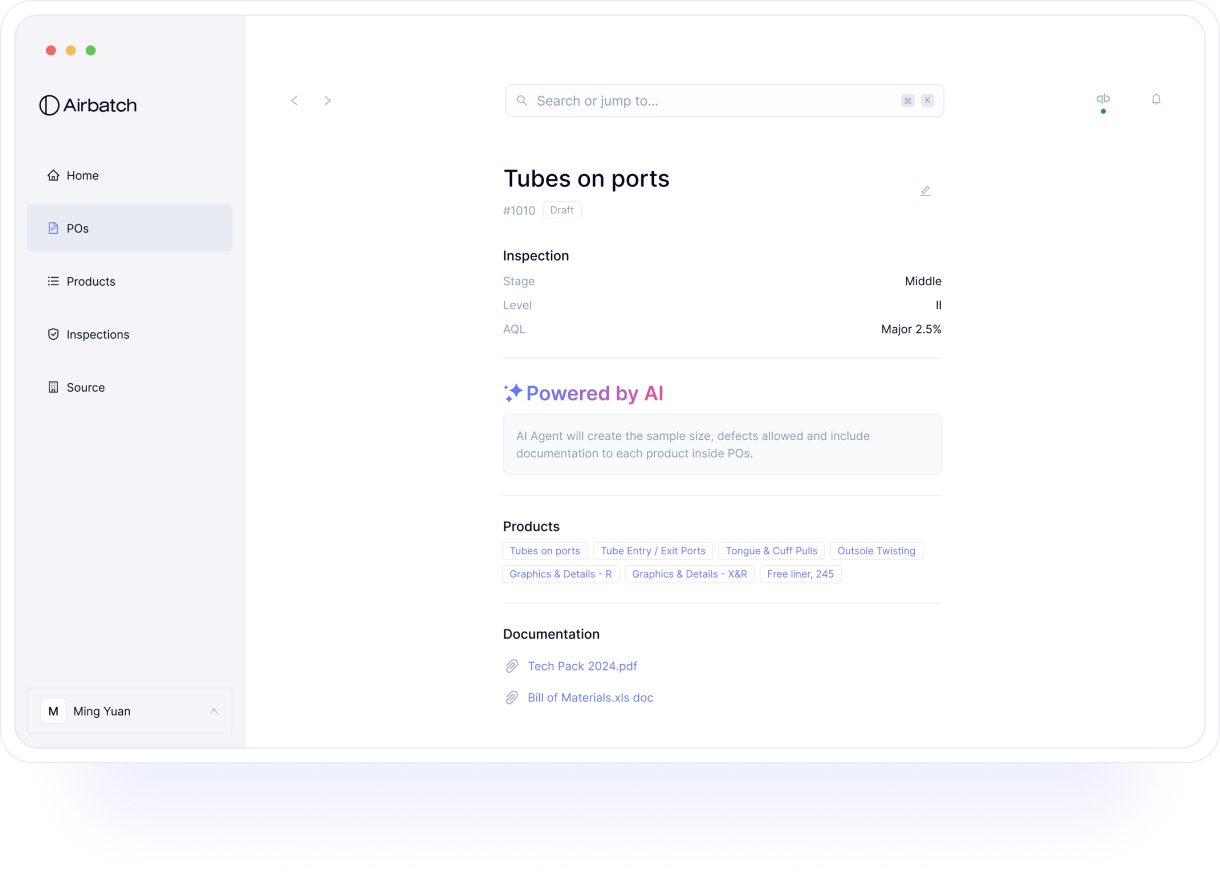
Analytics
Make decisions in real-time from data on product inspections and quality levels during each stage of production.
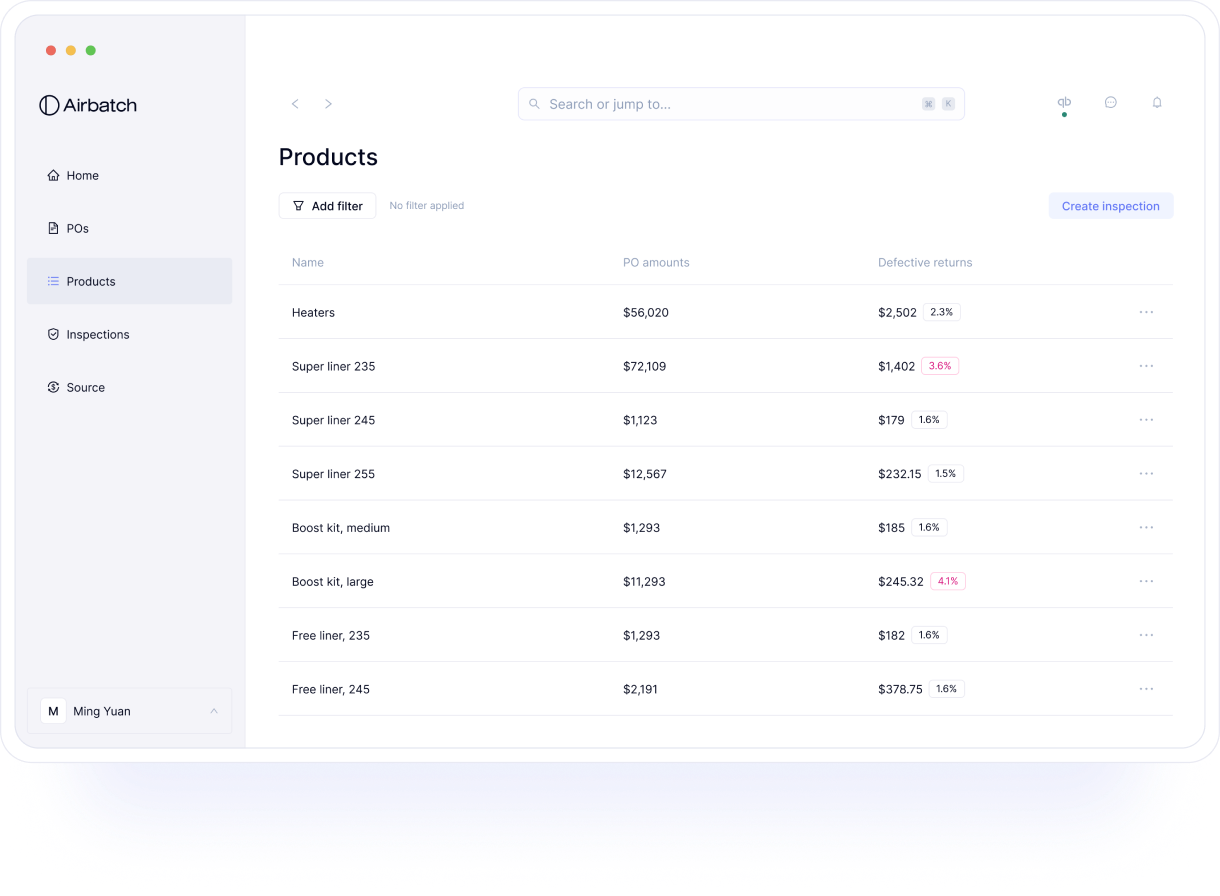
FAQ
Product sourcing is included for free under the Pro plan. Under the Pro plan you will get factory direct pricing and issue purchase orders directly to factories with no intermediary or mark up. Brands working directly with factories average a 30% reduction in product pricing.
Airbatch has built relationships with elite factories over the last 20 years. Elite factories maintain effective communication, adherence to strict quality standards, accurately assess risks, implementing robust mitigation strategies and improving quality processes.
Quality control focuses on identifying and managing potential risks to ensure the quality of products. It involves assessing and prioritizing risks, implementing measures to mitigate them and continuously monitoring and adapting strategies to maintain high quality standards.
Inconsistent product quality can lead to costly mistakes and lost customers. If products in a purchase order are made incorrectly, the financial consequences can be catastrophic. Inventory value is lost, customer return costs escalate and brand value is severely damaged.
The Airbatch platform automates product sourcing, product documentation, quality control processes and reporting. Most manual work associated with quality control happens automatically on Airbatch, empowering brands to scale the quality of their products without adding workforce.
Airbatch eliminates the expense and mark up of sourcing products, adding workforce to manage production, creating QC documentation, synthesizing inspection reports and in the end increase product margins.